Metal AM advances in composite tooling, Part 2
02 February, 2023
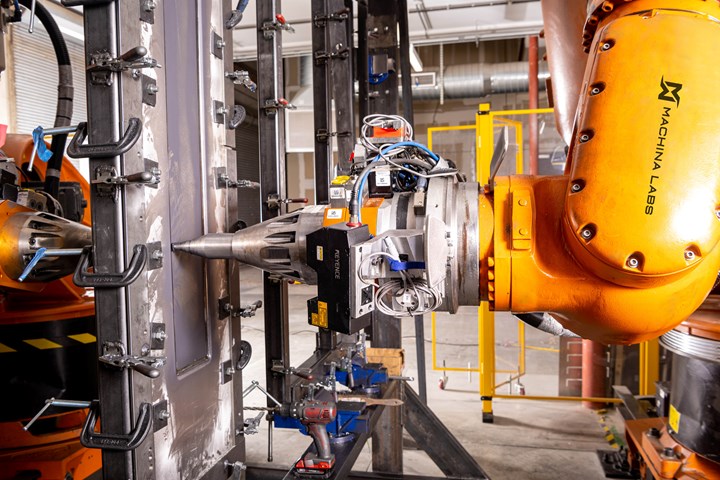
As reported in the December 2022 issue of CW, hard tooling is an important, potentially costly and often rate-limiting step in the process of bringing composite parts to market. However, advances in metal additive manufacturing (AM) over the past 15 years have given toolmakers, molders and OEMs many useful options for producing intricate mold components. And, with the advent of large-format AM (LFAM) technologies, it is now possible to print entire tools — albeit often single-sided only with necessarily simpler geometry.
Metal AM tools or tool components can cut weeks or even months off lead times without sacrificing accuracy or durability, and they often do so at lower cost than similar components produced via conventional manufacturing. Many processes also enable further functionality to be added to tooling or tool components, such as the use of conformal heating or cooling channels, which can shorten molding cycles and reduce part warpage.
In this report, we’ll continue our coverage of metal AM and other digital technologies and, as before, indicate which additional metal AM processes are production-proven — already used on tools producing commercial parts, often in high volumes — and which are close to or just beginning to be used on commercial programs.
Production proven: Hybrid extrusion/CNC machining
Although just starting to ship commercial printers to initial customers, the hybrid metal AM system designed specifically for toolmakers by Mantle Inc. (San Francisco, Calif., U.S.) has already been proven with key beta customers. These early adopters are all toolmakers, some of whom also mold, and have put the technology through its paces for the past few years to verify that printed and sintered mold components machine, EDM and weld just like conventional tool steels and are just as durable. At least one beta customer has used two inserts produced on Mantle printers to injection mold well over 2.8 million commercial parts for the personal care industry.
Mantle’s patented TrueShape process combines custom software plus an extrusion-based printer, which uses flowable metal pastes. It is also equipped with an integral high-speed CNC mill, which shapes and refines part geometry throughout the printing process. An important benefit is that operators needn’t know how to program additive or subtractive tool paths to use the printer.
The system takes imported CAD models, slices the geometry into layers and automatically generates additive and subtractive tool paths in G-code, which the printer then uses to produce a part. The extrudable pastes consist of metal particles of different types and sizes in a thixotropic liquid carrier whose viscosity can be tuned. The printer extrudes paste one layer at a time, followed by a short drying cycle to remove the liquid carrier, leaving a green body with the consistency of stiff foam. Next, a quick pass from the integral high-speed mill increases the accuracy and flatness of each layer. Typically, every 10 layers, the part is also contour milled to improve surface finish and refine features on the evolving part. Green body parts move from printers to Mantle’s furnace where they undergo an integrated debinding and sintering process to achieve final part density and geometry.
The company claims that its technology experiences the lowest shrink rate (8-10%) of any sinter-based metal AM process — as much as an order of magnitude less than other systems. Parts exit the furnace with excellent hardness, greater than 95% density and are ready to use after minimal CNC machining to help seat components in the tool’s master unit die (MUD). And unlike laser-based systems, sintered parts are said to have very low internal stresses, which helps the system hold very tight tolerances (±0.03-0.10 millimeters across a 102-millimeter part) and produce very high surface finishes (surface roughness (Ra) ~1-3 microns).
Currently, two paste formulations are available in widely used tool steels: H13, which offers the same metallurgy and performance as H13 hardened steel, and P2X, which provides the performance of P20 steel with slightly different metallurgy. The company says its material form factor eliminates the handling and storage issue of bare powders, and the high printing pressures and defects seen with filaments. Mantle’s pastes can also print thick-section parts unlike ink-based systems. With a build volume of 200 × 200 × 150 millimeters, the TrueShape process is said to be ideal for producing small- to medium-size mold components.
A good example of the types of mold components produced with Mantle’s system is a slide nose detail insert that industrial cutting-systems supplier, Hypertherm Associates (Hanover, N.H., U.S.) used in a study to compare injection molded part quality and wear for an insert produced conventionally versus one printed using Mantle’s system. Inserts were then used to injection mold 30% fiberglass-reinforced polyetheretherketone (PEEK) cap shields, which form a consumable torch stack-up used in a plasma cutter. H13 was specified for printed and conventionally produced inserts owing to that alloy’s high hardness (to resist fiberglass abrasion) and resistance to temperature cycling (PEEK is injected at 382°C into a tool kept at 179°C). The printed insert was designed to incorporate integral cooling channels to improve part quality and reduce cycle time.
Lead time to produce the printed insert was reduced 7-11 weeks versus the conventionally produced insert, and costs were lowered 75%. The printed insert required minimal grinding and wire EDM work to adjust the taper prior to seating it in the slide carrier. Hypertherm reports that molded part quality was the same with both insert types and no observable wear was identified after 50 shots.
“Compared with traditional manufacturing, Mantle’s technology is dramatically lower cost, it’s significantly faster and it enables the unique geometries that only can be made by 3D printing,” explains Ted Sorom, Mantle CEO and co-founder. “That combination of factors is what our customers get really excited about. The world is moving fast, technology is moving fast, but manufacturing hasn’t kept up with the pace of innovation. Mantle’s TrueShape changes that.”
Production-ready: Composite extrusion modeling (CEM)
There are many different printing systems on the market. Some print metals, some polymers, a few print composites and fewer still can print multiple categories of materials. One of the latter types was developed by AIM3D GmbH (Rostock, Germany), which has developed a novel extrusion-type printer that can print metals, plastics, composites and ceramics on the same printer as long as those materials can be supplied in a pellet format and converted into strands/filaments that fit through one of several different size nozzles. An open material system provides a broad range of printable material options while keeping production costs down, although AIM3D will also work with customers wishing to use proprietary materials.
AIM3D founders, then students at the University of Rostock, initially focused on developing a simpler and less costly metal AM printer based on the composite extrusion modeling (CEM) process, which is similar to fused deposition modeling (FDM) and selective laser melting (SLM). CEM was designed to use metal injection molding (MIM) pellets. After graduating and forming their company in 2017, the founders were asked by auto industry investors to try printing glass-reinforced polyamide 6 (GR/PA6), which led to development of a series of print heads and interchangeable nozzles using the fused granular modeling/fabrication (FGM or FGF) process to print neat or reinforced plastic injection molding pellets. The latest materials the team has printed are ceramics.
Because AIM3D’s process can print hollow-section parts, it can produce metal inserts with conformal cooling (or heating) channels. In fact, it’s said to be possible to print a part using multiple custom-formulated alloys, such as a high-hardness grade in combination with another of the same base alloy but infused with copper to enhance thermal conductivity without lowering the base metals’ sintering temperature. It’s also possible to print parts using the same metal but with different densities, modified by using pellets containing different particle sizes and thermoplastic binders. This enables material in one section of a part to sinter to a dense microstructure while material in another section sinters to a more porous microstructure. Hence, AIM3D’s system has an extra method for enhancing part functionality in addition to design/geometry and material selection.
Useful Links:
Source: www.compositesworld.com